September 24, 2022
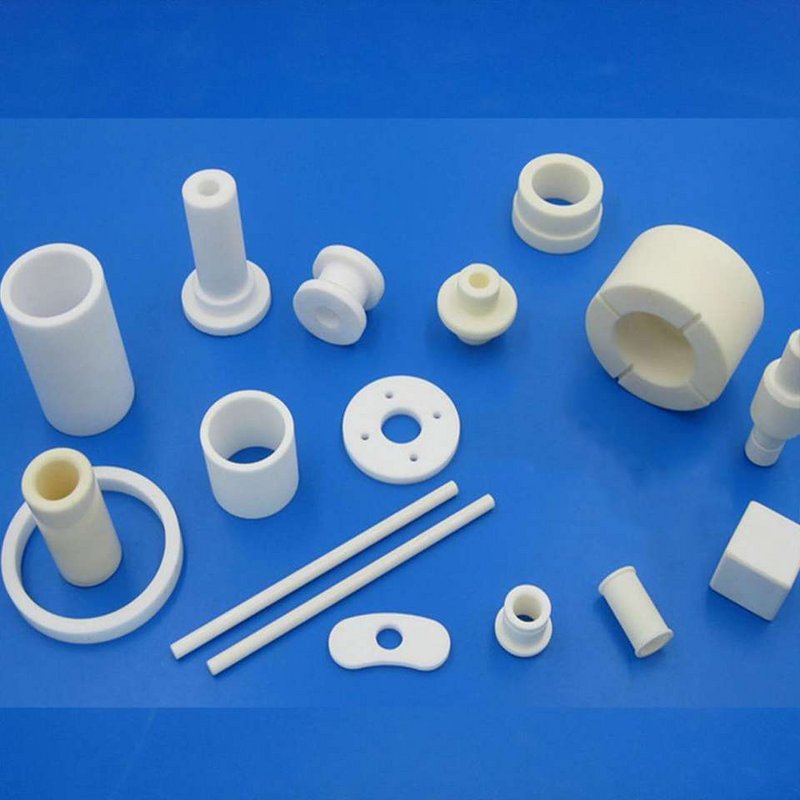
There are numerous advantages of using alumina ceramics in manufacturing
processes. Here are a few benefits: Low cost, high refractoriness, Resistant to
thermal shocks, and Machinability. Alumina is an ideal material for many
applications because of these advantages.
Low cost
Alumina ceramics aluminum oxide are a versatile material that is suitable in
a variety of applications. They are extremely resistant to corrosion and wear
resistance. Alumina of high purity is used in semiconductor production and
photolithography as well as for insulation.
Alumina ceramics are made by the process of dry pressing. This process is
ideal for making thin-walled products with a length to width ratio that is at
least 4:1. The material is processed using polyvinyl alcohol to binder during
the process. Alumina ceramics have superior mechanical and electrical
properties, and are employed in many electrical components.
High refractiveness
Refractoriness that is high in a ceramic material is the result of its high
machining ceramic content. Materials that are refractory with alumina content
exhibit lower thermal conductivity and higher heat capacity. They are employed
in numerous industries that need high heat-shielding performance.
In furnaces that use thermally corrosive materials, the ceramics must possess
high refractoriness. These kinds of applications aren't appropriate for porous
ceramic materials. Instead, they can be produced with greater density and less
porosity.
Resistance to thermal shock
Thermal shock resistance is one of the most important performance indicators
for solids operating in high-temperature environments. Thermal shocks can result
from random expansions and contractions of materials, which put stress and
strain on the structure. Energy conversion systems, electronic devices and
cutting tools can cause damage from thermal shocks. The thermal shock resistance
is usually determined by the maximum jump in surface temperature. The most
effective thermal shock-resistant materials are those that have low thermal
conductivity and a high coefficient of thermal expansion (CTE).
To determine the thermal shock resistance of solids an alternative model of
heat conductor that is not Fourier can be used. It is important to remember that
the thermal shock resistance of solids may be underestimated by Fourier heat
conduction. The non-Fourier model of heat conduct is more accurate and is able
to determine the thermal shock resistance of plates with thinner
thicknesses.
Machinability
While ceramic components
are extremely durable with outstanding mechanical properties as well as a low
temperature expansion coefficient, they are difficult to machine because of
their low material removal rates as well as their high wear on the tool.
Laser-assisted processing process can greatly enhance the ability to machine
Alumina ceramics. It also helps to reduce the wear of tools and cutting force.
It is possible to use an emulating model of the machining process. Alumina
ceramics are tolerant of high temperatures because they have the glass
interface.
Alumina ceramics are also renowned for their high hardness. They have a low thermal expansion coefficient meaning that even with high load, they'll retain their initial dimensions. This makes aluminas the ideal material for air bearings, precision valves wire-drawn components, as well as mechanical seal rings.
Posted by: Internet Marketing Line at
04:33 AM
| No Comments
| Add Comment
Post contains 507 words, total size 4 kb.
35 queries taking 0.082 seconds, 75 records returned.
Powered by Minx 1.1.6c-pink.